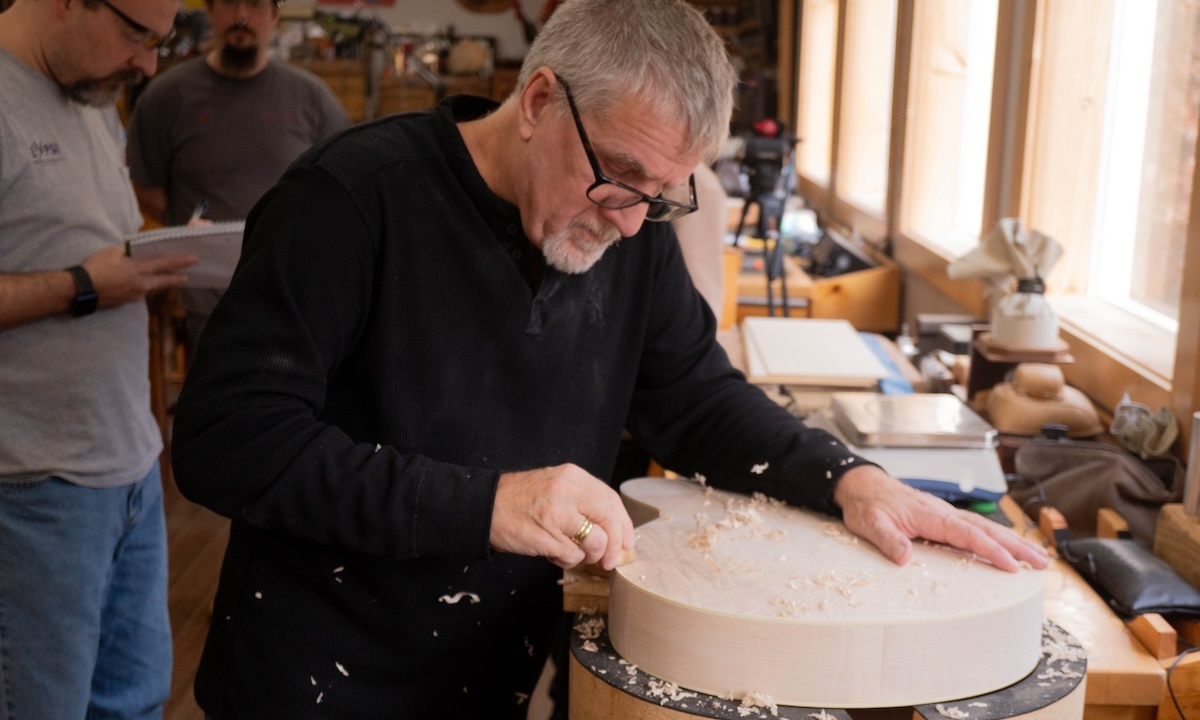
Luthier to the Stars
How Bryan Galloup built a world-class guitar-making studio in Big Rapids
By Craig Manning | March 1, 2025
He’s made guitars for the likes of Jeff Daniels and David Crosby, his instruments command five-figure sums, and he’s one of the nation’s most respected teachers of lutherie, the craft of building stringed musical instruments. Instead of writing that story from a music industry hub like Nashville or Los Angeles, though, Bryan Galloup has done it all from right here in Michigan.
Galloup owns Galloup Guitars, which operates out of a studio and workshop space in Big Rapids. The company houses both Galloup Studios, which makes, repairs, and rebuilds guitars on a contract basis; and the Galloup School of Lutherie, which seeks to “celebrate the art of guitar-making” by passing the craft on to the next generation.
So, how did Galloup end up becoming a luthier, a job he acknowledges to be extremely unusual in the modern world?
“For me, it starts with playing guitar,” Galloup says. “I grew up in a post ‘Beatles on Ed Sullivan’ world, so there were guitars everywhere. Everybody had a band. And so, like everyone else my age, I started playing music.”
While every childhood rock ‘n’ roll wannabe likes to imagine themselves achieving something akin to Beatles-level fame, Galloup quickly found his musical interests drifting elsewhere.
“I realized that my instruments just really weren’t performing the way that I wanted them to,” Galloup explains. “Having a little bit of a craft background—my father built houses and was a tool-and-die maker and a gunsmith—I started to work on my own instruments. Well, word got out, the next thing I know, I was working on other people's instruments, too.”
Despite inheriting some of his dad’s skilled trades acumen, Galloup says he was anything but a natural when it came to fixing up and improving guitars. “It was more like bloodletting,” he says of his initial adventures in lutherie. “But, thanks to my dad, I at least knew what not to do.”
For years, Galloup was just handling typical maintenance stuff, the musical instrument equivalent of “changing tires on cars, like re-fretting instruments and making changes to the bone nuts, saddles, and pickups.”
Before long, though, what had started as a hobby morphed into a passion.
“It just slowly segued to a point where [instruments] were all I thought about,” Galloup says with a laugh. “And once that happened, I decided to leave my dad’s tool-and-die shop and give it a go. That would have been in about 1980.” And so Galloup Guitars was born.
Acoustic Craft
As it turned out, Galloup’s slow burn toward guitar obsession culminated at the perfect time. The early 1980s had brought an explosion in the popularity of vintage guitars. The demand sent guitar prices through the roof, but it also opened a lane for skilled luthiers who could help buyers restore old instruments that hadn’t been properly cared for.
“That period is when all these old instruments that had been worth $125 or $250, they suddenly went to $1,000, went to $2,000, went to $4,000—and they kept going from there,” Galloup says. “And because of that, [lutherie] became a lucrative business just about the time I decided to stumble into it.”
Galloup Guitars rode that wave, with the business subsisting primarily on repair and restoration work. And while Michigan is “Gibson country”—Gibson Guitars, known for legendary electric guitar models like the SG and the Les Paul, started in Kalamazoo in 1894—Galloup’s specialty was in another iconic guitar brand.
“My sweet spot was acoustic instruments,” Galloup says, pointing to the Pennsylvania-based Martin Guitars. “I became quite good at restoring old Martin guitars, and a lot of those things became pretty valuable. I got really good at working on models from the 1930s and early 1940s, which was just a really great era for Martin.”
Galloup’s skill with old craftsman guitars became his calling card. Soon, UPS trucks were stopping at his business every day to drop off commissions.
How the Guitar Gets Made
As Galloup Guitars became an established name in the world of guitar repair, Galloup started getting a different type of phone call. Not only were people reaching out about his services, but they also wanted to learn why he was so good at what he did.
“I got something of a reputation for restoring instruments, and then people started reaching out to me and saying, ‘Hey, can I pay you to come and work with you and watch what you do?’” Galloup recalls.
Those inquiries led to the launch of the Galloup School of Guitar Building and Repair, which still operates today.
“At the beginning, it was kind of a disaster,” Galloup says of the school. “I didn't realize how disruptive it was going to be to have people in the studio observing me. But over time, I got better at it, and I started taking more students—first, for one week at a time, then a month at a time, then two months at a time. Before COVID, that school was up to 27 students at a time, rolling every two months, and we’d been full for at least 10 years.”
The pandemic hamstrung the school’s ability to operate, and Galloup has downsized that part of his operation in the aftermath—“We’re down to about 16 students per class,” he says—but is still passing down lutherie skills to the next generation. From beginners learning the basics, to experienced craftspeople mastering technical sides of the craft, Galloup’s classes cater to students at every stage of their guitar-building journey.
Strumming a New Tune
Speaking of journeys, Galloup didn’t actually start building his own guitars until the mid-1990s. For the first decade plus, restoration and repair work were so in demand that Galloup Guitars had little time to do anything else. In fact, it wasn’t until Galloup brought students into the fold that he saw any reason to broaden the business.
“As the school grew, I realized that I didn’t have enough repairs to keep up with the demands of the school and what I needed to demonstrate,” Galloup says. “I started having the students build guitars so they could get all the lessons. That set the hook in me of building guitars. I said to myself, ‘If I’m running a school teaching people to build guitars, I’d better get pretty good at it.’ And I also thought that, if I was going to make it a guitar building school, it sure would be nice if my guitars were competitive on the open market.”
“Competitive” is one word you could use to describe Galloup’s instruments. The base price for one of his guitars is $18,000, most go for $25,000, and certain custom models have exceeded $38,000. Right now, the wait time for a guitar from Galloup Guitars is two years.
Both the price tag and the wait time, Galloup acknowledges, would be jaw-dropping for the average person. Once people learn what goes into a designer guitar, though, they might be less gobsmacked.
The Power of Tone
The biggest differentiator, Galloup says, is the wood.
“I specialize in Brazilian rosewood, which, if you don’t have your paperwork, [is] not a legal wood,” Galloup explains. “Mine is CITES (Convention on International Trade of Endangered Species) protected, and I have the CITES paperwork for it, which makes it very valuable. But I don’t use it just because it’s valuable; it’s also the best-sounding back and inside wood for an acoustic guitar. It’s very brittle, it’s oil-free, and it’s incredibly responsive. It sounds like iron.”
For the soundboard (the front of the acoustic guitar), Galloup takes annual trips to Italy and Switzerland to hand-select so-called “tone woods” for his instruments.
“I go right to the source, I sit down, and I take a couple of days,” Galloup says of that process. “The tone woods used on my instruments are not standard at all. They’re definitely custom-selected.”
Also not standard: the process for turning these rare woods into actual playable instruments.
“Every component of my guitar is taken to a specific thickness or thinness,” he says. “Each piece of wood being different, all those thicknesses vary. You have to know what thickness to take it to in order to get it to respond. Even the braces on the inside of the guitar, every one of those is hand-tuned and hand-voiced to get maximum response.”
All that painstaking work may be lost on a guitar beginner, but Galloup says seasoned players can hear and feel the difference—hence their willingness to pay big money and wait two years to get their hands on a Galloup-made instrument.
“$25,000 is a lot of money, but if you think about the most serious musicians in the world, playing guitar is how they spend their time,” Galloup says. “The way I look at it is this: A world-class musical instrument will make the player do things they wouldn’t normally do. It inspires them, because really, it’s a conduit for getting what’s in their head out into the musical world. For people like them, it absolutely is worth that money.”
Trending
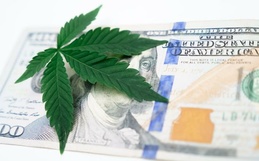
Michigan’s Marijuana Tax at Work
Cannabis has become a big business in northern Michigan, and local governments are putting tax dollars earned from dispensar… Read More >>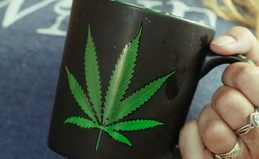
California Sober: Why People Are Switching from Alcohol to Weed
They call it “California sober.” Generally speaking, this term applies to folks who use marijuana but abstain f… Read More >>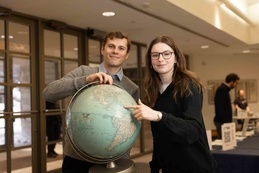
The Legacy of Student Activism
“It’s a physical letter to your representative,” Alex Tank says when asked to define the word “prote… Read More >>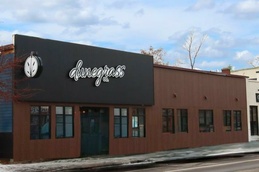