
LEAN ... on the Farm?
How Japanese auto manufacturing is changing the way one local farm works.
By Eric Cox | May 11, 2019
Atop the high, breezy hills east of Wolverine sprawls a fairly nondescript 40-acre farm owned by Dan and Wendy Babcock, northern Michigan farmers who place a high value on the integrity of the food they produce, consume, and sell.
Obviously missing in the greening landscape of Serendipity Farms are the hard lines of fixed fencing that normally border such properties. Here, animals don’t traipse around the same patch of ground day after day, month after month. At Serendipity, the fencing, like the animals it contains, is mobile — a key feature of the pasture-based animal management plan they use.
The Babcocks rotate their animals like many grain farmers rotate crops — in ways that don’t overburden or decimate the soil.
Take the Serendipity chickens, for example. Their loitering areas change periodically. Fencing is moved and the brood with it. The area they were once confined to is left naturally fertilized and all but picked clean of bugs by the hungry birds. And, since the birds are eating lots of natural food, they’re also ingesting lots of nutrients, making their eggs and meat more nutritious, said Wendy Babcock.
Hogs, too, get a respite from the square pens in which they’re traditionally kept. At Serendipity, the swine are fenced off in a marshy woods, where they’re allowed to root and wallow ceaselessly. Their foraging churns up the earth and decimates the dense undergrowth, opening the forest floor up to the sunshine and new growth.
Across the farm, cows amble past donkeys. Guinea fowl roam about in pairs while a throng of little black piglets chase their mother and seek shelter in her girth at the slightest hint of danger.
To the untrained eye, Serendipity Farms might look sparse and disjointed. But a closer look reveals an intricate plan.
The Babcocks are using safe, sustainable egg and meat production methods in their growing farm-to-table food business. Aside from their coveted Animal Welfare Approved certified management methods, Wendy employs a production scenario that got its start in the world of Japanese auto manufacturing.
That’s right — Japan. Car manufacturing.
In her endless quest to bring Serendipity Farms into an efficient, profitable, but above all else responsible entity, Wendy reached into the far east to improve her family’s Midwest operation. Her quest to streamline the farm’s meat and egg production led her to the Toyota Production System, often called LEAN manufacturing.
Though this method was borne of Japan’s massive auto production industry, the heart of this method’s primary mission — waste reduction — is an outcome sought in many businesses, not just car making.
To Babcock, the LEAN way is central to her operation, providing a disciplined framework, the principles of which are helping her reduce costly redundancies, curb waste and the cost and labor associated with managing it, and, most importantly, focusing on the integrity of the products she offers customers.
The 51-year-old former barrel racer called on an anecdote to illustrate her point.
She said wintering her flock of egg-laying hens resulted in hours of extra labor because, since the birds couldn’t go outdoors, they stayed in their pens and nesting boxes when they pooped. Ordinarily that might not be a big deal, but since the eggs are to be sold later, they have to first be washed.
That, of course, meant Wendy was forced to stand over a sink, scraping and scrubbing the eggs clean. That’s a bunch of extra time and a lot of water. Plus, handling the eggs more resulted in increased accidental breaks — another waste.
Carefully considering the problem, the couple settled on a pretty ingenious solution: re-purpose an old piece of plastic into a door the hens could use to access the pasture throughout the winter.
It worked.
The chickens spend more time outside relieving themselves. The eggs are cleaner. Wendy’s time cleaning pens and scraping poo off eggs, and extra water required to do so, are saved. Likewise, fewer eggs are broken since they don’t have to be handled and scraped as much.
The little move they made with the re-purposed plastic is a great example of lean production. Thoughtful consideration of a problem yielded a very low-cost-high-effect solution that not only saved them time, but also improved the product (eggs) by keeping them cleaner throughout the production process.
According to Wendy, lean farming has nothing to do with efficient farming. “You can be efficient at wasting. You can be efficient at overproducing,” she said. “There are all kinds of ways being efficient is anti-lean.”
Overproduction, she said, is one facet in which efficiency runs afoul of LEAN protocols. Though it may satisfy a farmer to see an enormous haul of summer hay, for example, overproducing hay can result in several problems. Without immediate buyers for that hay, the extra product must be stored and kept fresh, often at added expense to the producer.
LEAN principles help farmers streamline goods, producing just enough to satisfy demand, but not so much so that the excess must be stored or otherwise handled. Babcock said the excess hay, while perhaps providing an ego boost to the grower, creates more downstream waste — waste that could’ve been avoided had lean methods been employed.
All these lean procedures are aimed at one thing, though: improving the end products for customers who value Serendipity Farms’ certified non-gmo and no soy production scheme.
It’s working, too. The farm sells fresh eggs, broiler chickens, grass-fed and grass-finished beef, turkey, pork and goose. Babcock Farms honey, maple syrup, organic smoothie packs microgreens and vegetables — all produced in the family’s thoughtful, natural way, are available at the farm store.
To learn more about the farm and its LEAN methods, visit www.serendipity-farms.com.
SIDEBAR
A Little More About LEAN
As small farmers in America strive to make ends meet in a climate of continually shrinking margins, many, like Dan and Wendy Babcock, are looking for ways to streamline their operations, improve value and reduce waste.
Developed by Japanese industrial engineers at Toyota between 1948 and 1975, the Toyota Production System (TPS), the framework for LEAN farming, places prime consideration on eliminating production waste in virtually all its forms. From underutilized workers to overproduction, TPS — sometimes called “just-in-time production” is aimed at conserving resources.
The philosophy has been adapted to the farm model, in which many of the same principles are brought to bear in reducing waste while boosting value and, ultimately, quality.
Farmers who employ lean principles make sure their tools and implements are all stored in the same place. More importantly, they are returned to their proper places after use. It seems absurdly simple, but, according to Wendy Babcock, that simple practice saves her a bunch of time and frustration, since she doesn’t have to spend valuable minutes looking for a lost tool and fretting over it.
Transportation, as well as inventory, process, production, staff training and customer feedback are all carefully considered so that the best, least wasteful method can be applied.
Once the lean principles are in place, the workload should be more streamlined, with customers enjoying the best products possible because every step in its production has been been “leaned.”
The model can be applied to all sorts of endeavors, not just manufacturing or farm production. Lean principles can be applied to the organization of one’s garage, for example, or a restaurant.
Trending

A Bird's-Eye View of Skegemog Raptor Center
Photo by Tyler Franz On a cold, rainy April day in 2021, James Manley received a phone call about an injured bald eagle nea… Read More >>
Trailblazing Women Take the Stage
As we wrap up Women’s History Month, Great Lakes Center for the Arts is paying tribute to three of country music&rsquo… Read More >>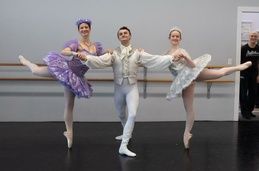
Sleeping Beauty Ballet Dances into Traverse City
The Northwest Michigan Ballet Theatre brings a new classical interpretation of The Sleeping Beauty to Dennos Museum’s … Read More >>